The essence of deploying 3D vision systems for robots in pharmaceutical, automotive, packaging or assembling industries is to increase operational efficiencies, reduce errors and increase output. Every industry works differently from the other; so are the objectives of integrating 3D+AI robots into a company's operating systems.
A robotic vision system is an interconnection of various intelligent systems and components for the purpose of image capturing and analyzing. Machine vision systems are used in almost every industry to identify, inspect, calibrate and count products and parts. Every movement and action an intelligent robot performs is controlled by training modules in the deep learning program fused with the vision system.
How Do Robotic Vision Systems Work?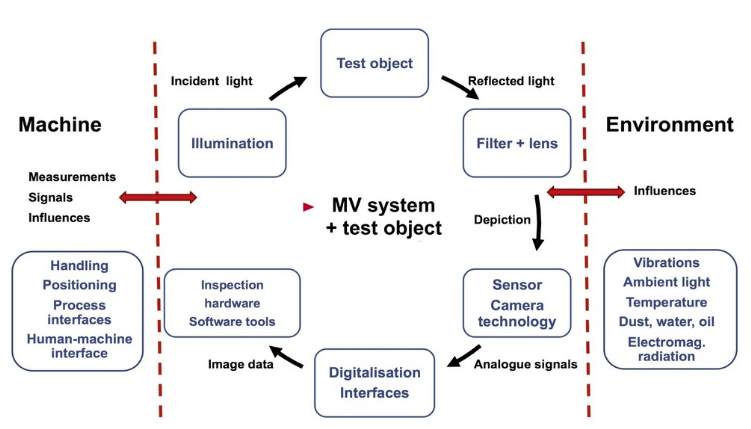
For robots to perform complex tasks like detecting defects, picking parts with more precision, scanning codes and counting parts, the robot's arm is equipped with a 3D vision system.
Sensors feed on the vision system to detect the presence of an object which then triggers a light source and illuminates a light on it. Now the 3D camera captures the objects' images. After a 3D vision camera captures the object image, image processors process the image into a digital image. The data is relayed to the robot's software for analysis. For a robot to pick the objects better, the software carrying image data is trained using robot training modules using a deep learning communication interface.
What are the components of a machine Vision system?
An intelligent robot can pick air compressor parts and assemble them, label and pick steel bars. They are also used to glue and then grease swing bearings in a production line. For a robot to perform the above industrial tasks, a series of well-coordinated activities are first carried out in the machine vision system. This system is composed of various components programmed to serially communicate with each other.
2D or 3D Camera
The camera is the first component of a machine vision system. 3D vision cameras are responsible for capturing parts' images. 2D or 3D cameras provide an in-depth field of view for the image sensor to process and relay accurate aspects of the object.
The industrial environment poses great challenges to the effectiveness of robot 3D cameras. Factors such as vibration, lighting, temperature and dust are worth considering when choosing a machine vision system. Choosing the right 2D OR 3D camera determines the robot's machine vision system adaptability to harsh environments.
The quality of a robotic camera is determined by its resolution. A high resolution 3D camera like the Mech-Eye LSR L 3D camera will produce a digital image with more pixels and thus high object detection accuracy.
Lighting
Lighting is a critical component of a machine vision system. It determines the quality of features captured by the camera. While some industrial 3D vision cameras can perform well under different point clouds, others will require adjusting the light intensity to better functionality.
Communication Interface
The entire machine vision system is controlled by a communication interface. All the communications between the vision systems to the controlling software system are passed through the interface. For smooth continuity of industrial processes, data output from the vision processing system is passed to machine vision software for better coordination.
Stages of Machine Vision System
Every stage in a machine vision system is systematic. From detecting the presence of an object to relaying digital images, every step is well calculated.
Step 1. Image Detection and Illumination
Once the robot system is set, objects within the range are detectable, a sensor detects the object, and light is illuminated on them. This sets the next phase for the robot's 3D vision camera to capture the objects' images. This stage is the foundation for the success of all the subsequent processes.
Step 2. Image Capturing and Processing
With the environment set for image capturing, a sensor triggers the camera to capture the object image. The image aspects are digitized by a digitizing device and then transmitted to the installed machine vision software for storage and processing.
Step 3. Digital Data Communication
Instructions to be commanded to the robot are provided by communication protocols set out at the digital data communication stage. The output from the vision processing system is communicated to the software programs.
How Mech–Mind AI + 3D vision systems help in intelligent robot solutions
Mech-Mind AI+3D vision robotic solutions cover diverse industrial applications. Mech-Mind machine vision systems are used in manufacturing industries to depalletize and palletize boxes. Other industrial solutions offered by Mech-Mind AI+3D vision systems include:
Machine Tending
In machine tending, intelligent robots are used in manufacturing companies to tend to machines in automated processes. With programming software, the robot loads materials into a machine and offloads the finished product or part. With machine tending, production output is high; cases of injuries are low and cost-effective. Mech-Mind's AI+3D industrial robotic solution was incorporated into the brake disk production line to help tackle the challenge of light interference, reduce injuries and boost productivity.
Assembly, Locating, and Gluing
Assembling companies have taken advantage of intelligent robots to accurately detect, pick and assemble component parts at high speed. In automotive, manufacturing companies have changed from manual wheel installation to automated robot wheel installation. This has led to increased productivity and reduced operational costs and errors.
Piece Picking
Piece picking is a labor-intensive task characterized by low speed and errors. With AI + 3D vision-guided robots deployed to pick and pack goods, the issue of counting errors is solved, efficiency is high, and the high output becomes the norm. In e-commerce, piece picking and counting are the main activities. In this illustrated e-commerce use-case of Mech-Mind's AI+3D industrial robotic solution, the company can integrate robotic solutions with set logistics systems thus creating a smooth operation across all the systems.
Conclusion
Intelligent robots have changed how companies used to operate by automatic operation processes. The flaws that characterized traditional systems were resolved by AI + 3D vision robotic solutions offered by Mech-Mind. As proved in our use cases, our solutions cover manufacturing, assembly, construction machinery, and logistics. For more consultation, please contact Mech-Mind experts.