Is your factory constantly having unexpected production downtimes? If your company has been experiencing lots of those recently, you may be experiencing significant losses in revenue. There are plenty of solutions you can utilize to solve the underlying causes of your equipment downtime.
With that being said, here's everything you need to know about reducing machine downtime in your factory below.
How to Recognize Downtime in Manufacturing?
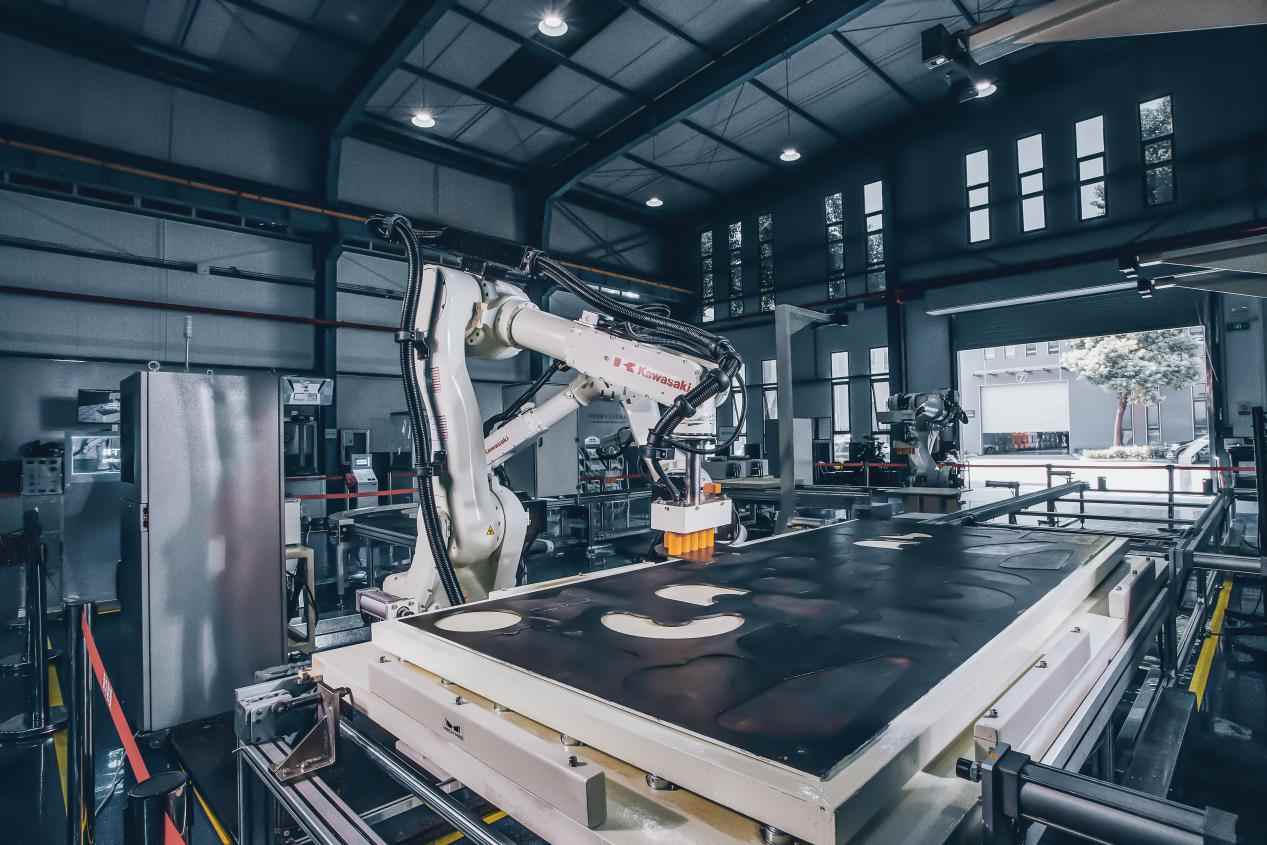
Downtime in manufacturing is when machines cannot work for production. Production downtimes in a factory involve all stops occurring during the production period. And these shutdowns often result in huge revenue losses for businesses.
Generally, production downtime is split into two classifications below:
Planned Downtime: Scheduled downtimes are implemented to conduct machine maintenance and product changeovers. This type of downtime is considered budgeted halts in production.
Unplanned Downtime: This type of downtime occurs when machines suddenly fail to function as planned. Unplanned downtimes often happen due to unexpected occurrences taking place. These include machine breakages or shortages in used materials.
How Much is Downtime Really Costing Your Factory?
The cost of downtime in manufacturing varies. For instance, the cost of downtime in food companies is different from that of automotive manufacturers. But a study conducted by Vanson Bourne indicates that approximately $250,000 every hour is lost due to unexpected downtimes.
But to have a better idea of how much exactly downtime is costing your factory, you can always calculate downtime manually. For optimal results, it might be better to invest in automated machine data collectors. After all, manual machine downtime tracking may not provide up-to-date and accurate data.
What Causes Machine Downtime?
Machine downtime happens for a wide variety of reasons. To find out why, you may need to go through several rounds of inspections in detail. Here're three main causes of machine downtime:
Errors made by operators: If there are not enough workers in a factory, they might be assigned to multiple machines. And with so many machines to tend to, your employees might end up being overworked, making them much more prone to making mistakes, especially for precision instruments.
Lack of machine maintenance: Not regularly maintaining your machines may also lead to unplanned downtimes. Or your factory's machines aren't properly maintained. In these cases, the possible damages to your equipment could worsen, leading to more extended unplanned downtimes.
Part failures in machines: Sudden failures in machines also lead to machine downtime. And related to the said reason above, your machines might be vulnerable to more failures if it is not being maintained and inspected as needed.
How to Reduce Manufacturing Downtime?
There are various ways you can utilize to reduce manufacturing downtime in your factory. Here they are.
1. Make regular equipment inspections and maintenance schedules
One way to ensure that your equipment doesn't undergo unexpected downtime is to regularly have them inspected and maintained. By doing scheduled checks and maintenances, you can quickly identify possible problems earlier before they worsen.
2. Ensure your employees undergo simple machine maintenance training
Besides creating the necessary schedules, you must also ensure that your employees are trained to perform easy machine maintenance tasks. These tasks include cleaning, lubricating, and fixing simple machine problems. That way, they can help out in unplanned downtimes, especially if the unexpected issue can be solved using simple fixes.
And with readily available workers to fix simple problems, you won't have to wait for professionals to solve your issues. This, therefore, greatly saves your time and even reduces your machine downtime in the process.
3. Upgrade your manufacturing equipment
More advanced technology usually means a more powerful production capacity. Especially for medium and large factories, it is essential to upgrade the production technology and equipment in time. When some equipment is too old or difficult to handle production demands, the problem of machine failure is prone to occur. Taking the time to update your factory equipment is very important to enhance your factory competitiveness and vitality.
Furthermore, Mech-Mind AI+3D solutions lead to more reliable intelligent operation systems in piece picking, machine tending, and many more applications that will greatly assist your workers. And by using the best AI and 3D solutions, you can ensure that your factory will suffer a lesser cost of downtime by making it intelligent and data-driven.
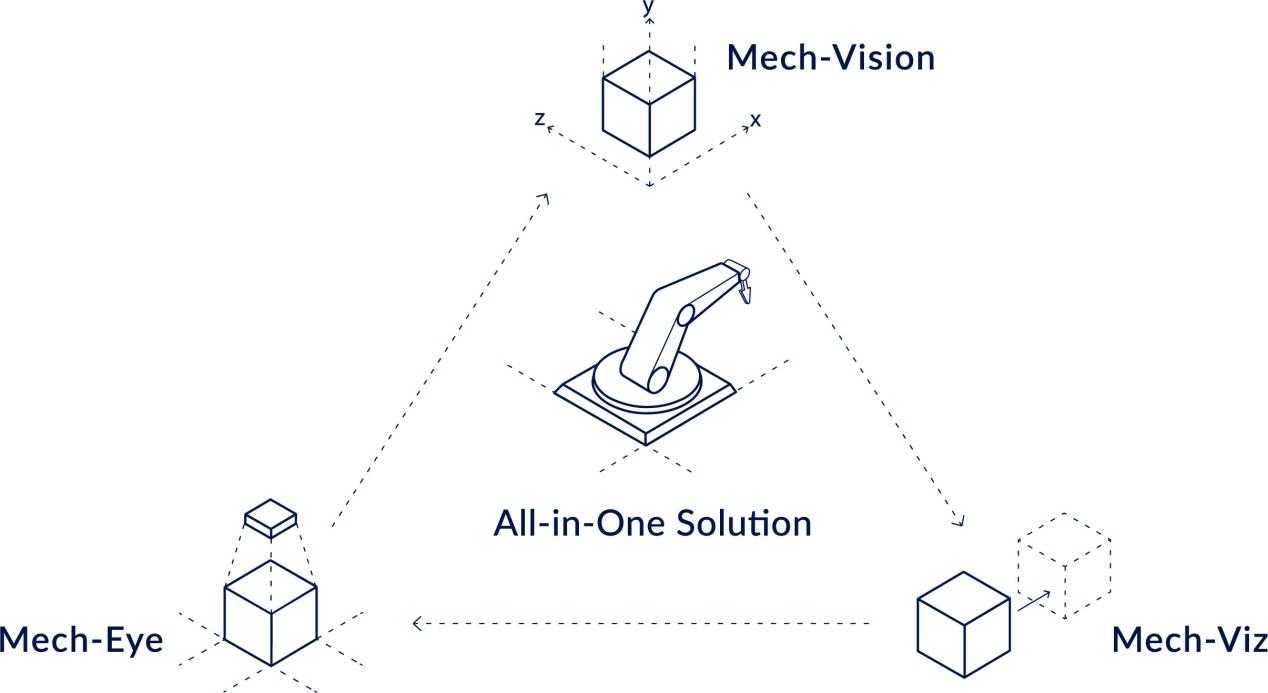
4. Implement intelligent robotics technologies
Automated machinery factories have become a trend in recent years. Intelligent robotics technologies can relieve some of the workload of workers. As we know, robots can perform mechanized, simple operations better in terms of endurance. Mech-DLK software provides high-precision deep learning algorithms for robots, empowering them to operate with higher speed and improved accuracy. Moreover, this platform software is very user-friendly and totally visualized, which can effectively reduce operational errors.
Final Thought
Having unplanned downtimes is unavoidable, but it's essential to reduce their frequent occurrence in your factory. If your factory is experiencing equipment downtime frequently, it's important to identify the underlying causes first to figure out the best solutions to reduce unexpected production downtimes. And one great solution for the lesser cost of downtimes is to upgrade your equipment with Mech-Mind excellent robotics solutions.