Robots are loaded with 3D cameras integrated with machine vision software to detect and track objects using a vision system. This vision software is fused with advanced algorithms to enable object detection, tracking, and positioning.
A robotic vision system comprises 2D or 3D cameras or even sensors that communicate with algorithm modules created by the software. For robots to detect and recognize objects, the robot has to be trained on the same, and the data stored in deep learning algorithm modules. With the communication among all the vision systems configured correctly, the challenges of object counting, verification, tracking, and recognition are solved.
Object detection and tracking in robotics are gaining more popularity in industrial applications and warehouse automation processes. Besides increasing production rates and minimizing errors, object detection systems are today used to aid in stock control management in supermarkets and warehouses.
What is Object Detection and Tracking?
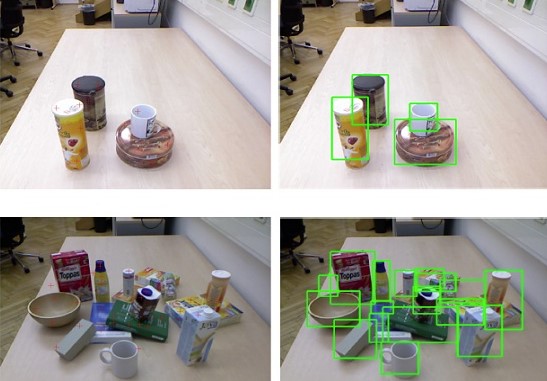
Object detection refers to a robot coupled with vision and image processing technology to recognize the presence of an object in an image or video.
Object tracking refers to the steps in which a robot performs object detection, recognition and tracking of items along through an image processing application. Motion planning using software programs integrated into AI vision algorithms makes object recognition, and tracking more precise.
What is the Importance of Object Detection and Tracking?
Maximizing Accuracy and Uptime Speed
Object detection and tracking by AI + 3D robotics in industries increased accuracy in bin picking, detection, depalletizing and palletizing. And with consistent speed, which results in more output. In manufacturing companies where robotics utilizes vision systems to scan items, monitoring stock levels in each product category is more accurate.
High Return on Investment
Manual tallying of items is characterized by errors. In this era of e-commerce, replacing goods on return is expensive and leads to repetitive tasks. Employing a robotic object detection system in e-commerce stores eliminates errors, which increases return on investment.
High Cost Performance
Intelligent robots are commanded through AI systems, and both require less cost to maintain. Automating object detection tracking results in a high output rate and low operational and maintenance costs.
Enhancing Seamless Operation
Time taken to search and scan product codes manually leads to loops in operations. Object detection using deep learning is fast and well-coordinated. This eliminates loops and creates a seamless flow in operations.
How Do Robots Detect and Track Objects?
Robots fused with machine vision system detects and tracks objects through data representation modules actuated by machine learning algorithms. 3D cameras or sensors equipped on robots scan objects on sight with high precision and high speed no matter the variation, position, and orientation. After objection identification, robot motion paths are automatically calculated to enable the robot to detect objects while avoiding collisions.
The detected object on motion is then tracked using an object tracking model created by algorithms. Different technologies are fused together to create a systematic communication between the 3D cameras and sensors and the AI algorithms. Speed is of essence to maintaining continuous tracking of objects on trajectory forms.
What Makes Object Detecting and Tracking Difficult?
1. Change in Object Aspects Ratios
Robotics are first trained on objects for tracking purposes. Any future change in object aspect ratios and sizes confuses the object tracking algorithms. Any alteration of item aspects makes tracking difficult. This challenge is common in supermarkets and e-commerce store where item detection and tracking is done by robots.
2. Multi Priorities
Precise item tracking entails monitoring trajectory speed, positions, and real-time tracking. Configuring the tracking algorithm and image processing data to achieve accuracy in the three aspects makes tracking a challenge.
3. Background Distractions
Backgrounds used during object training may sometimes differ from the real background used during tracking paths. This inconsistency negatively impacts the accuracy of tracking models. Using not too busy backgrounds makes item detection and tracking easier for AI and deep learning systems.
4. Object Collisions
Collision of objects may cause appearing and disappearance of the object in the created tracking path. Therefore, object collisions do not only make tracking difficult but monitoring object positions a challenge.
Mech-Mind: The Advanced 3D Vision System for Robots Object Detecting and Tracking
Mech-Eye Industrial 3D Camera
For any robot to detect and track objects, it has to be equipped with smart 'eyes' to identify the presence of an item. Mech-Eye Industrial 3D Camera is the robot's special 'eyes'. The 3D cameras capture 3-dimensional images in point clouds and communicate them to the tracking algorithms.
In the automotive industry, a Mech-Eye industrial 3D camera is used to track and recognize randomly placed different-sized hatch doors along a contour and glue them.
Mech-Vision Machine Vision Software
Mech-Vision system contains many different vision algorithm modules and tools for creating and editing object trajectories. For accurate tracking, Mech-vision is also used to pose and adjust the position of the items. Robots with Mech-Vision carry out depalletizing and palletizing duties with the help of advanced algorithms that can accurately identify and track objects.
Mech-DLK Deep Learning Software
All deep learning modules training, including instance segmentation, image classification, object detection, and semantic segmentation are done by the Mech-DLK. Once the deep learning module training is complete, Mech-DLK integrates all the training and stores the data. The multi priority tracking challenge in robots is solved by Mech-DLK. You can integrate module training to identify, detect, position and track objects simultaneously.
Mech-Viz Robot Programming Software
Mech-Viz has a 3D simulation software tool for motion simulation. In addition, Mech-Viz system has an inbuilt path planning and collision algorithm. The algorithms also carry out object tracking to avoid collisions along the created paths.
What are the Other Functions of Machine Vision Systems in Robots?
Measurement
Machine vision systems with smart 3D cameras rely on 3D imaging to calibrate with precision measurements of objects. After a machine vision system has acknowledged the presence of an object, 3D cameras like Mech-Eye Industrial 3D Camera calculates the distances between two points to understand object size.
Counting
After object inspection, the robot's machine vision system used for stock control and management identifies product codes and counts them. In the piece picking process, a robot with machine vision will pick the desired number of SKUs and place them in order bins.
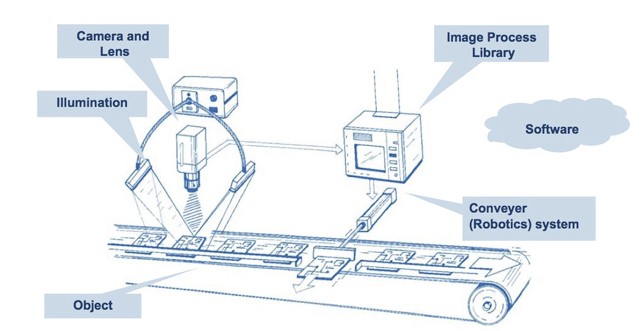
Positioning
Arranging items or parts to be in the same orientation is a function of a machine vision system. In industrial applications, the location and orientation of items placed in a bin for labeling and scanning by AI + 3D robots are communicated through the robot's machine vision system. The robot then realigns and positions the items in the correct orientation.
Conclusion
Robots with modern machine vision systems have resolved many industrial challenges and improved efficiencies along production lines.
Mech-Mind has revolutionized how industries operate by providing advanced machine vision products to detect and track objects. With the Mech-Mind vision system, robots can locate, identify, pick, and calibrate objects accurately and as desired. Mech-Mind expands the capacity of industrial robots to perform complex and risky tasks in industrial settings. If you need a robotic machine vision system or an all-in-one solution to solve manufacturing or warehouse challenges, don't hesitate to consult our experts at: info@mech-mind.net.