Mech-Mind AI + 3D Vision Solution
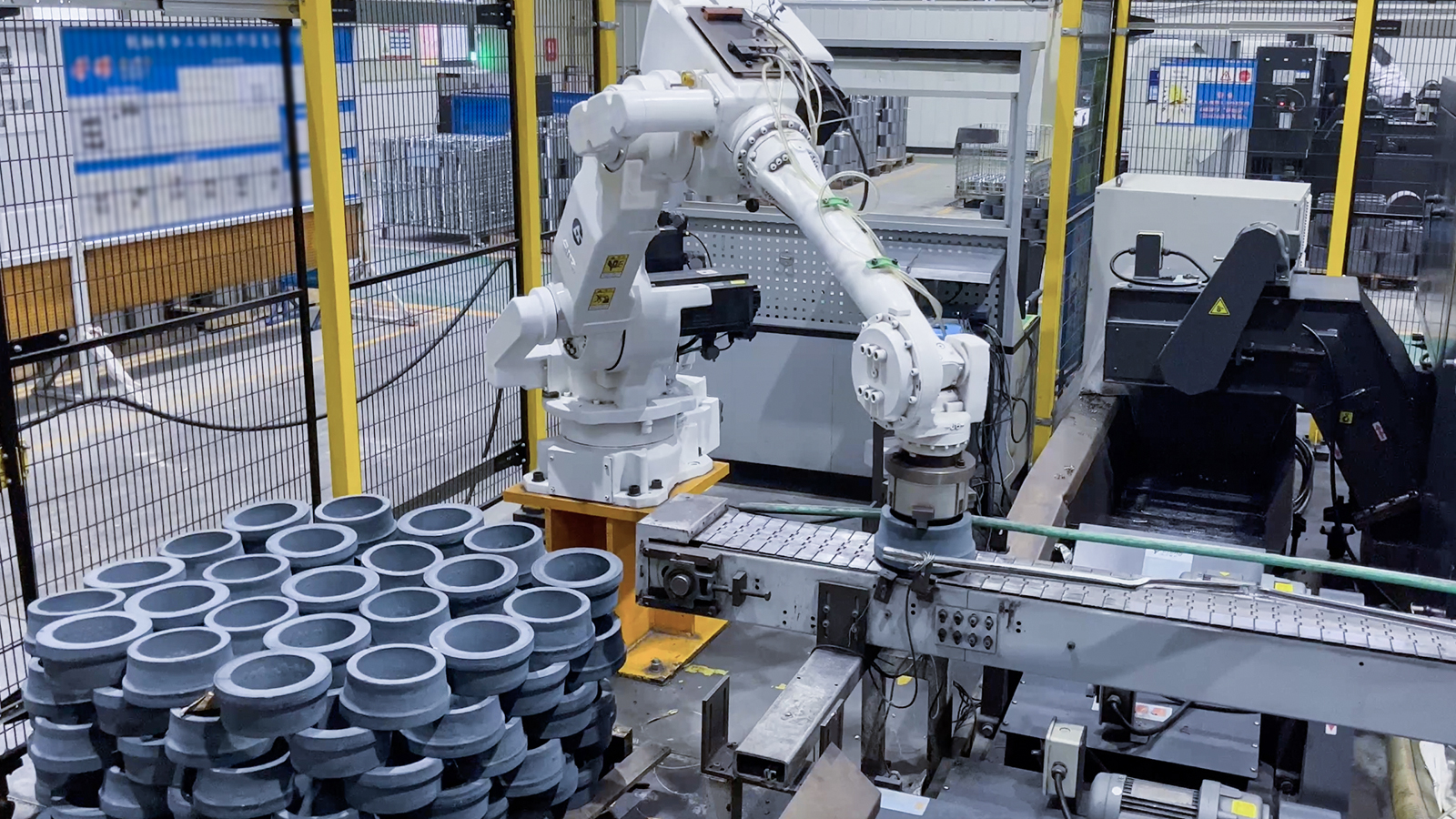
The workflow:
1. Mech-Eye LSR L-GL promptly captures images of the bearing inner rings on the pallet. Then, the vision software processes the images taken by the camera.
2. Using the coordinates provided by the vision system, the Mech-Viz robot programming software autonomously plans trajectories for gripping bearing inner rings.
3. The robot turns towards the conveyor line, placing the workpiece onto it. Simultaneously with the robot's motion, the Mech-Eye 3D camera (stationarily mounted) captures images, shortening the overall cycle time.
4. The robot picks up and places the workpieces from each layer, first picking up those stacked in the forward orientation, then those in the reverse orientation, repeating this process until an entire pallet is emptied.
The solution:
Mech-Eye LSR L-GL
1. Features high precision and a wide field of view, generating high-quality point cloud data for bearing inner rings with dark-colored surfaces and severe slag.
2. Effortlessly handles typical on-site environmental light interferences.
The 3D vision system
1. Distinguishes between the stacked orientation (forward and reverse) of bearing inner rings, ensuring seamless unloading and loading operations.
2. Easily accommodates various specifications of bearing inner rings.
The result:
1. The factory has achieved automated loading of workpieces onto the conveyor line.
2. Enhancement of production efficiency due to the shortened cycle time.