Customer Requirement and Project Info
The vision-enhanced robots should autonomously depalletize totes loaded with raw products, pour the raw products out of the totes, and stack the empty totes on a pallet.
The totes are arranged in 5 layers, with 6 totes per layer, and are transported by an AGV to a specific location. Then vision-guided robots perform depalletizing, material loading, and palletizing. Before implementing AI + 3D vision solution, employees had to perform all these tedious and repetitive tasks manually.
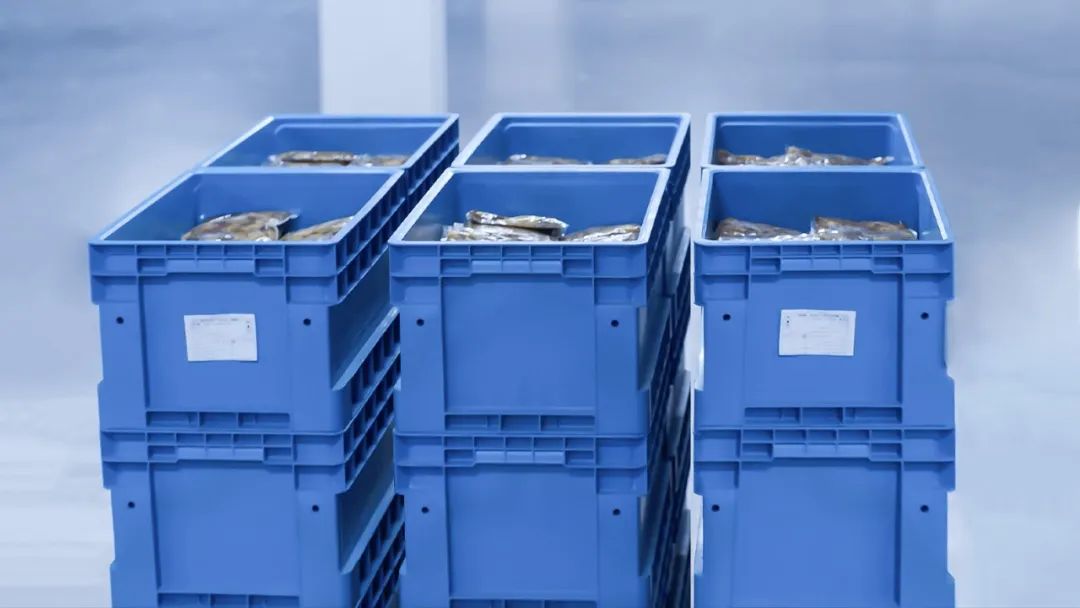
AI + 3D Vision Solution
① The 3D vision system locates the totes fast and accurately and guides the ABB robots to perform accurate depalletizing.
② ABB robots pour raw products out of totes to where they will be further processed. Then 3D vision system guides ABB robots to stack the empty totes on a pallet.
Performance
Recognition success rate: > 99.9%
The Proven Results
1. Single production line increased production by 100%
2. Up to 40% reduction in manufacturing cost per piece
「 Project Details 」
Equipment Included
○ Mech-Eye industrial 3D camera
○ Mech-Vision machine vision software
○ Mech-Viz robot programming software
○ ABB IRB 6700 industrial robots
Why AI + 3D Vision Solution
The Mech-Mind solution combines AI technology and 3D vision with ABB robots to help food & beverage manufacturers streamline and optimize manufacturing processes, guaranteeing employee safety and rigorous quality standard, saving labor costs, and meeting growing production demand.
▕ Meet Increased Production with Accurate Depalletizing & Palletizing
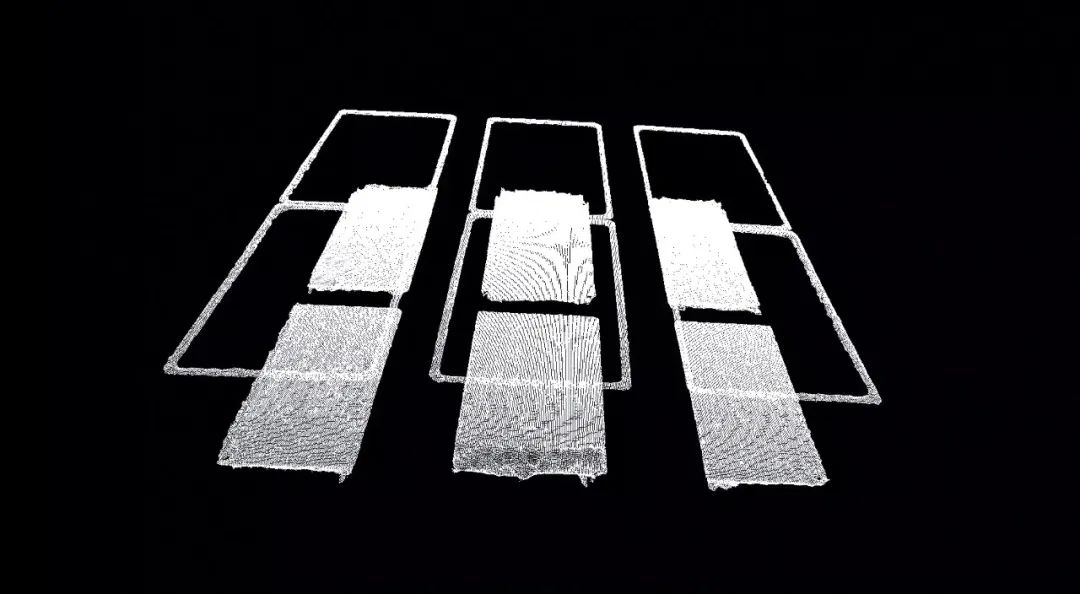
○ The Mech-Eye industrial 3D camera generates accurate and high-quality point clouds of totes with thin walls and uneven surfaces.
○ Mech-Mind's 3D vision system identifies the exact location of each tote and calculates pick points for robots, ensuring accurate picking.
○ When palletizing empty totes, the 3D vision system identifies the tiny limit blocks on the metal pallet to ensure that the robot can accurately place the totes into the limit blocks.
▕ High-Speed Processing for Shorter Product Cycles and Higher Output
○ The 3D vision system can obtain the position of totes by taking a single image and collecting partial features, which is highly efficient.
○ The image acquisition time can be as low as 0.5s, fulfilling the customer's production requirements.
○ Vision-guided robots pick totes in pairs, improving depalletizing efficiency.
○ 24/7 stable operation extends the production time significantly, improves output, and ensures the timely delivery of orders.
▕ Flexible and Fast Application Deployment to Reduce Costs and Downtime
○ By mounting on the robot arm, one camera can image both the depalletizing station and the palletizing station, which is highly flexible and reduces deployment costs.
○ The collision detection and path planning algorithms autonomously calculate the proper robot motion path, guaranteeing stable operation in compact space.
○ Mech-Eye provides multi-language and multi-platform SDK options. It is compatible with GenICam and supports Halcon and more.
○ Integrating Mech-Eye with Mech-Vision and Mech-Viz, users can deploy various typical applications right away.