Piece Picking is one of the fastest growth areas for robotic applications. It has been a part of manufacturing processing for a few decades, initially performed by humans, and now increasingly being served by robots. Even though piece picking is possible without 3D scanners, there are some situations where extremely accurate imaging using cameras, such as the Mech-Eye industrial 3D cameras, can play a crucial role in more accurate and dependable piece picking.
What is piece picking?
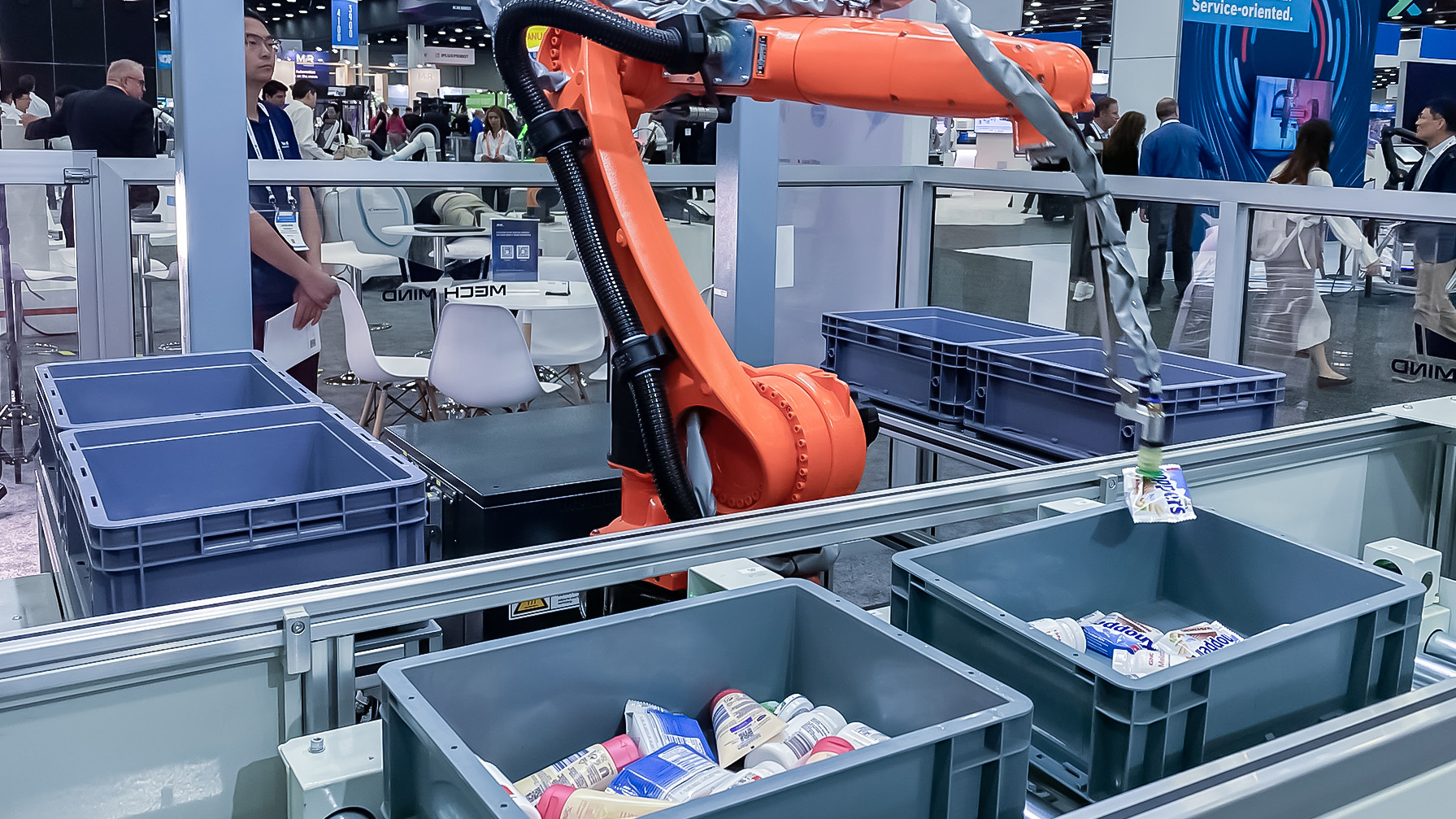
Piece picking is an order fulfillment process in which individual items from an order are selected and placed into a container or carton before being shipped to customers. Robotic piece picking, on the other hand, refers to the process in which intelligent robots automatically retrieve a wide variety of SKUs from an inventory bin and then deposit them into an order container. Robotic piece picking is a crucial component of automated order fulfillment.
Applications Across Multiple Industries
While we typically associate piece picking with selecting various individual items, it finds applications in multiple industries, including those listed below:
• E-commerce
• Grocery
• Third-party logistics
• Health & Beauty
• Pharmaceuticals
Meeting the labor shortfall, providing better jobs
It's a prevailing theme in manufacturing and industry that robots often handle tasks that are unfulfilling, dirty, and potentially hazardous. Piece picking is a labor-intensive activity known for its slow pace and susceptibility to errors. It can be considered one of the most monotonous tasks while also demanding a high level of accuracy to minimize human errors.
Challenges
Challenges in Automation:
While robotic piece picking offers significant improvements in productivity and quality assurance, it has limitations in its conventional form. It relies on a highly specific set of tasks and how items are presented to the robot. Without adequate 3D vision, the robot is essentially blind. If an item is not placed precisely where the robot expects to find it, there is a high likelihood of a missed pick, potentially causing a stoppage that requires operator intervention. This dependency on items being correctly placed in parts trays or avoiding accidental displacement poses a challenge to automation.
Challenges in Effectiveness:
3D scanners play a crucial role in capturing images of target objects, especially in piece picking. Industrial cameras provide a wide field of view for the image sensor to accurately process and relay information about the object. The industrial environment presents significant challenges to the effectiveness of robot 3D scanners. Factors such as vibration, lighting, temperature variations, and dust should be considered when selecting a machine vision system. Choosing the appropriate 2D or 3D camera is crucial in determining the adaptability of the robot's machine vision system to harsh environments.
Benefits of high-quality 3D scanner in piece picking
Compared to two-dimensional image processing, utilizing 3D vision systems can indeed be more demanding in terms of software, time, and processing power. However, this increased demand is effectively addressed by the use of 3D algorithms, multi-core processors, and a variety of software tools, which significantly enhance their ability to meet the requirements of various industries' production lines.
With this extended capability, 3D vision systems are now applied to a wide range of tasks that 2D vision systems cannot perform. These tasks include:
1. High-precision assembly
2. Measurement of volume, flatness, thickness, and height
3. Surface tracking and robot guidance
4. Digitization and object scanning
5. Piece picking
6. Mixed depalletizing and palletizing
Piece picking, for instance, remains a challenging test for various vision systems due to the robot's need to learn how to grasp items accurately. Moreover, it must account for size variations and different measurements. Consequently, clear and precise visualization of the part is essential.
3D vision processes all this information in real-time with the utmost precision and accuracy, even when encountering changes in scene dynamics or dealing with parts that are dark, reflective, shiny, or light-absorbing. It accomplishes these tasks efficiently, regardless of the item's orientation or position within the bin.
Conclusion
Piece picking is already prevalent in various industries, and in most cases currently, it is fair to say 3D cameras are not in use. The past few years have seen the advent of affordable, high-quality 3D scanners that are fast enough to offer immense flexibility and deliver attractive productivity gains that far outweigh the initial cost of the 3D camera. A camera that can perform to such high standards must also be of a true industrial grade so that it can tolerate industrial situations. The Mech-Eye industrial 3D camera is that camera.
The flaws that characterized traditional cameras were resolved by Mech-Eye industrial 3D cameras offered by Mech-Mind. As proved in our use cases, our scanners can make piece picking easy work. For more consultation, please contact Mech-Mind experts at info@mech-mind.net.